FilterPress Filters
Filtration Process
FilterPress filters The filtration process with filter presses is a filtration within the scope of sediment filtration.
It works with the principle of separating the clean liquid by keeping the solid parts in the filter press cloths, in the separation of the solid and liquid parts in the fluids of different densities and viscosities, which are generally formed by liquid and solid components.
Depending on the nature of the process, the main product that will result from the filtration process may be liquid or solid part.
As is known, Cartridge and Bag type filters also work for the same purposes.
Filterpresses are mostly used in fluids with high solids content, that is, in fluids with high solids load, and in fluids with high density and viscosity. The reason for this is to extend the change period of the filters by obtaining a higher filtration area with filter presses.
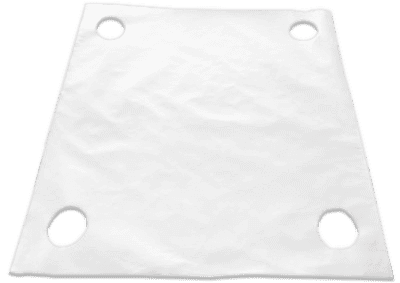
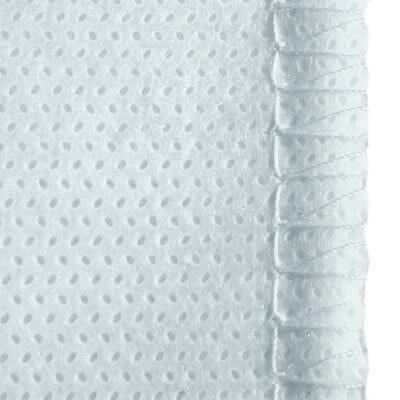
When a cartridge filter or a bag filter is used in fluids with the same solids %, that is, with a high solids load, even if the capacity of the filter housing and the cartridges and bags it is placed in is sufficient in terms of flow rate, the container (house) in which the filters are placed will be lost in a short time due to the solid matter height. requires frequent replacement.
Since this is an undesirable situation, the replacement periods are extended by using larger volume cartridge filters or bag filter housings by increasing the volume of the cartridge filter or bag filter housings.
For this reason, in some processes, filterpresses, belt filters or vacuum rotary drum filters are used for fluids with more than % solid matter and high density and viscosity.
Since belt filters and vacuum rotary drum filters are filters with movable mechanical parts, they may malfunction from time to time or create some operating difficulties. In addition, the solid product coming out of these filters is in the form of wet cake. It contains some process fluid.
Filterpresses do not have continuously moving mechanical parts. After the first cloths are attached, they are used by compressing with the hydraulic compression mechanism. When it is time to change the clothes, the liquid inside is emptied by blowing with pressurized nitrogen or air or in another way, depending on the process. Plates are opened by operating the hydraulic mechanism, dirty cloths are removed and new filters are attached. By operating the hydraulic mechanism again, the plates and filters are compressed and the filterpress is activated.
Because of their ease of use, operation and change, filter presses are more practical and useful than belt filters and rotary drum filters.
Specially manufactured filters called “filterpress cloth” or “filterpress filter” are used in filterpresses. Filterpress filters are in a wide variety of types, shapes, sizes and micron properties that vary according to the structure and characteristics of the process used.
In our company, all types of filter press filters are produced with the features required by the process you need.
FilterPress Filters
Chemical Resistance
Filter Material | CONTINUOUS OPERATION TEMPERATURE ro | PEAK TEMPRATURE co | STRONG ACID | WEAK ACID | STRONG ALKALINE | WEAK ALKALINE | OXIDIZING SUBSTANCE |
POLYESTER | 130 | 150 | GOOD | PERFECT | WEAK | MIDDLE | PERFECT |
POLYPROPYLENE | 90 | 105 | PERFECT | PERFECT | PERFECT | PERFECT | WEAK |
GLASS FIBER | 280 | 320 | GOOD | GOOD | MIDDLE | GOOD | PERFECT |
POLY TETRA FLOR ETHYLENE (TEFLON) | 240 | 280 | PERFECT | PERFECT | PERFECT | PERFECT | PERFECT |
ACRYLIC | 120 | 140 | GOOD | PERFECT | GOOD | GOOD | GOOD |
COTTON | 90 | 115 | WEAK | MIDDLE | GOOD | PERFECT | MIDDLE |
POLYAMIDE (NYLON) | 100 | 120 | WEAK | MIDDLE | GOOD | PERFECT | 0 |
TYPE OF MATERIAL | 185 | 200 | PERFECT | PERFECT | PERFECT | PERFECT | GOOD |
POLYESTER | 200 | 260 | MIDDLE | GOOD | GOOD | MIDDLE | GOOD |
POLYPROPYLENE | 240 | 260 | WEAK | MIDDLE | WEAK | PERFECT | WEAK |
FilterPress Filters
Product Selection Recommendation
The following are the factors to consider when defining, selecting, and processing the filter press cloth:
- Type of filter fabric (considering the parameters in the table above)
- The structure of the filter fabric (nonwoven, monofilament woven, multifilament woven etc…)
- Desired micron grade
- Layers of filter press cloth and features of each fabric layer separately
- If each layer has micron degree or gram/m2 weight values, air permeability and longitudinal strength values
- Entry-exit directions considering these layers
- Width x height
- Technical drawing, location of holes, dimensions, distance to edges
- Requested additional operations and features.
It is useful for companies that demand filter press cloth from our company to define the above features regarding the filter press cloths they need.
FilterPress Filters
Usage areas
- In the filtration of process fluids in the chemical industry
- In the filtration of fluids with high solids content, ie solids load
- In wastewater filtration
- In the filtration of treatment sludge
- For separating liquid and sludge in muddy process fluids
- In drinking water, process water, cooling water and waste water filtration
- Oil, milk, beverage filtration in the food industry
- In the filtration of industrial oil and hydraulic fluids
- In metal coating filtration processes
- Sediment filtration in paint, varnish production
- in filtration processes in the pharmaceutical and healthcare industries
- Beer, wine, juice etc. in the production processes of alcoholic and non-alcoholic beverages
- In the filtration of liquids containing oil, milk, various solids and pulps in the food industry
- In the cosmetic industry and filtration of biological process sludge
- In the filtration of industrial and hydraulic fluids
- Printing inks and printing related filtration processes
- Metal plating, galvanization, nickeling, filtration processes in the cataphoresis system
- In the filtration of polymeric liquids and solutions
- Sediment filtration in paint varnish production
- In the filtration needs of biochemical and biotechnological processes
- In the filtration of sludge from domestic and industrial wastewater treatment systems
- In sludge and waste dewatering plants Separating waste in meat and slaughterhouse facilities
- In hazardous waste disposal
- In the filtration of document sludge, paint shop and oily wastes in the metal sector
- In various recovery processes
- In the energy sector and in the filtration of cooling tower sludge, coal removal processes
- Filtration and disposal of sludge in water treatment processes
- In the electronics industry, electrolysis baths and filtration of metal hydroxide sludges
- In recycling processes of machine oil, waste oil and fuel oil
- In refineries and petroleum chemical industry
- Solvent production and recovery
- In the mining and gold refinery sectors,
- In marble quarries, marble and artificial marble production facilities, in the separation processes of clay, kaolin, concentrated mines, bentonite, dolomite and drilling mud
- In the porcelain and ceramics industry,
- In the porcelain and ceramics industry,
- in the glass industry
- For filtration needs in the paper industry